Cracks in your drywall or plaster interior walls could be the result of your house settling (which could come from the foundation) or may be the result of earth movement, according to Gregg Cantor. The Home Mender shows us how to remove a buckled seam from a ceiling or wall, apply new tape and mud. Click the links to see what's inside 'Dustin's Toolbox'.
Cracks in ceilings may be cosmetic or they can be a structural “red flag”. The difference depends on the shape, size, location, and the cause of the cracks.
Often we don’t even realize there are cracks and when we do notice them, we don’t know how old they are; did they just happen, or have they been there for years? Once the cracks are noticed, then it’s a good idea to do a little investigation into them. It is not uncommon for homes to get a crack or two in their ceilings over time, therefore older homes will generally have more ceiling cracks.
New homes will often develop a few cracks in the first year or two, but most of them will be at door and window corners or at the areas where the walls meet the ceilings, rather than on the ceiling itself. One of the common reasons for this is that many homes will settle a little in the first year or two. Also, the wood framing lumber usually drys out some which causes the studs, joists, and rafters to twist or bow slightly. Major track builders know that they will get a number of calls about these cracks in the first year or two and just consider it part of the construction business.
Hairline and spiderweb type of cracks
If the crack is near any woodwork or trim, cover with painters’ tape to protect the surface. Next, use the utility knife to cut a v-shape notch the entire length of the crack. Clear any debris from the cut (a shop vac could be handy). Step 2: Apply Drywall Tape. Apply 1/8 inch of joint compound over the crack and embed a strip of drywall tape. “Cracks that cause concern are those which run across the length of a ceiling and then continue down a wall along the same line,” writes Tim Anderson of SF Gate Home Guides. This is a sign of structural damage, usually related to a weak wall stud or perhaps something that was jarred loose in an earthquake or the settling of the home over.
Hairline type of spiderweb cracks due to paint issues
When repeated coats of paint are applied over other coats, then over a period of years, the chances of crazing (a pattern or network of hairline/ fine cracks) or alligatoring (a pattern similar to the reptiles scaly skin) cracking increases.
The layer(s) under the topcoat get brittle over time and expand and contract due to thermal and moisture changes differently than the more flexible topcoat. These lower coats tend to crack first and then the cracks work their way up to the topcoat, thus patterns of thin cracks develop in the topcoat of the paint.
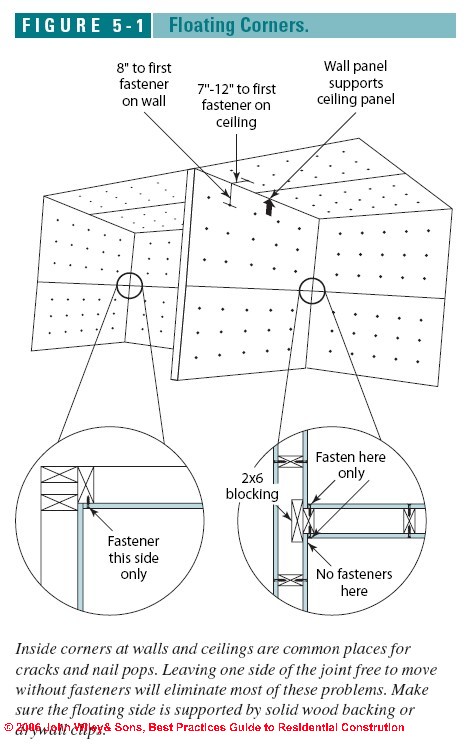
Spiderweb or hairline type cracks due to drywall mud issues

At drywall joints where two pieces of drywall butt up to one another, drywall installers tape the joint areas. Drywall tape is used as well as drywall joint compound, often called drywall “mud”. If the drywall joint compound is put on in one or more coats that are too thick then when the mud dries, it shrinks, creating hairline spider or crazing type cracks. When too much water is added in order to thin the mud prior to application, small hairline cracks may also occur. These types of cracks are merely the result of poor workmanship.
Straight cracks at taping joints
Cracks that appear at the side of drywall joint tape are usually caused by improper mud application during the installation. When the drywaller taped the joint they did not use enough mud and this can result in shrinkage cracks along the tape lines.
Usually, the crack will be very straight because it is following the straight edge of the tape at a drywall joint. This is insignificant for structural concerns and is instead evidence of poor workmanship.
Cracks on a sagging or bowed ceiling
If a ceiling is bowed, sagging, or dropped down, then the reason may relate to structural issues. Common causes include:
1. Spacing of ceiling joists or trusses
If the ceiling joists or trusses supporting the ceiling drywall are spaced too far apart, then sagging may result and the stress from this may create cracks.
2. Improperly sized ceiling joist
When the ceiling joists or trusses are undersized for the drywall ceiling weight that they are carrying, then sagging may result and the stress from this may create cracks.
3. Damaged ceiling joists or trusses
Occasionally, a ceiling joist or a truss becomes damaged or cracked, this weakens the framing member and the ceiling will bow or sag in one or more areas. Thus, stress is placed on the drywall and cracks develop.
Cracks caused from a load-bearing wall being removed and not having proper supports installed
Bowed ceiling cracks may also be caused by a load-bearing wall being removed without the proper structural support being added. At times the ceiling may not be bowed, but one section has dropped down. This movement can result in cracks. Read more on load-bearing walls.
Cracks caused by truss uplift
Cracks that appear where a ceiling intersects a wall may be due to “truss uplift”. Roof trusses tend to move a little when there is a seasonal change of temperature or humidity. These fluctuations and changes may result in the trusses moving or shifting a little. This is common and most homes are engineered to handle movement due to truss uplift.
Truss uplift cracks are normally noted on interior walls, not exterior walls. The cracks will typically appear on walls that are perpendicular to the direction that the trusses run. Generally, these cracks are not considered to be a structural concern and may even open up and close somewhat depending on the season. Read More On Truss Uplift.
A higher level of concern with ceiling cracks occurs when:
A crack is continuous through the wall and ceiling
Cracks that run across the ceiling to the wall and then down on the wall, basically a continuous crack going through the ceiling and the wall, may be a concern. This type of crack suggests that there may be a structural issue i.e. a foundation or framing issue.
Ceiling cracks running diagonally across the ceiling
A crack (of a 16th of an inch or larger) that runs at a diagonal angle through a sheet(s) of drywall requires a lot of force to create this crack. It’s like the drywall is ripped apart. This type of crack generally would be considered a “red flag”, depending on width, length, and location.
Wide cracks and areas that have a number of cracks
Ceilings that have multiple cracks that are more than just a small hairline crack are a concern. Cracks that are 1/8 or 1/4 of an inch wide or more would easily fall into this category. A crack that is 1/8 inch wide and only two feet long in a corner will not be given as much weight as a ceiling with 1/4 inch wide cracks, three or five feet long and that appear in a number of locations.
Ceiling cracks become more of a “red flag” if there are other signs that the house may have movement or structural problems
When ceiling cracks become a concern you should look for other factors that indicate possible structural issues to determine the severity and importance of the ceiling cracks.
Signs of possible structural issues include:
- Cracked foundation or slab (Read more)
- Sloping or sagging floors
- Doors and windows that stick or won’t open
- Sagging roof
Cracks may also be caused by:
- Small earthquake tremors
- Settling of the home
- Soil movement from slope creep or landslides
- Sinkhole issues
Bottom Line
Ceiling cracks are common and usually not a major concern. The older the home, the more likely for cracks to appear. Most contractors and homeowners will view cracks as a maintenance or cosmetic issue. Occasionally ceiling cracks can be a “yellow” or “red” flag that there is a serious or structural issue, therefore it is good to be able to recognize warning signs that a problem may exist.
If you are unsure if there is a problem or if a ceiling crack is serious, a home owner or buyer may wish to consult with an appropriately qualified professional. This may be a framing, drywall, or general contractor. A structural engineer likewise may be helpful in providing meaningful information.
- You may only need preventive maintenance
- If very minor, then you may just need to monitor it for changes
- If repair is needed, it is much cheaper to correct it in the early stages than after it has become a big problem
- Should it be major, then you may need to consult a qualified professional
Take a minute and review our page with other common structural issues in homes
Articles and Resources On Common Structural Issues In Homes
Additional Resources
Cracks develop in wall and ceiling areas. What are they a sign of and what can be done?
Contractors will tell you that concrete cracks; well likewise, stucco tends to crack. There are several things...
If a load bearing wall is removed, there are structural issues and risks that homeowners and buyers should be aware of.
Settlement may cause damage to a house, but some settlement can be prevented or reduced.
Floor creaking may be related to the installation of the floor or to the homes foundation settling. Other reasons include...
If your foundation has a crack or cracks know what to look for to determine if they are major or minor.
Sloping floors are often one of the warning signs that structural engineers look for when analyzing a house.
Doors that self close or open is usually not due to a ghost. First check if floor is level.
Can you name the type of foundation that you have?
- POST a QUESTION or COMMENT about plasterboard cracks, drywall cracks, gypsum board cracking & movement
InspectAPedia tolerates no conflicts of interest. We have no relationship with advertisers, products, or services discussed at this website.
Drywall cracks in ceilings or walls:
Where, when & why does drywall crack? Coefficients of thermal and moisture expansion & contraction or movement for gypsum board products.
This article describes the common causes of all types of cracks that appear in drywall or gypsum board or plasterboard walls & ceilings in building interiors. Illustrations show where cracks are most likely to appear, explain why, and suggest both repair approaches to drywall cracks and how to prevent cracking in plasterboard or gypsum board.
Photo at page top: severe settlement cracks around windows in an Alaskan home. Soil, foundation, and frost problems were causing severe ongoing movement in this structure.
We also provide an ARTICLE INDEX for this topic, or you can try the page top or bottom SEARCH BOX as a quick way to find information you need.
Causes & Types of Cracks in Drywall, Plasterboard, Gypsum Board Walls & Ceilings
Article contents - Causes of drywall or gypsum board cracking, sorted by categories
- DRYWALL CRACKS
- TRUSS UPLIFT, ROOF - separate article
Gypsum Board Installation Error contribution to gypsum board cracks & damage
Drywall installation snafus: poor support or connections, over-cuts with a drywall knife at corners of openings, failure to provide for seasonal or other variations in temperature & moisture, improper joint finishing, possibly omission of drywall tape at some gaps, cracks, or repairs.
Drywall movement control joints omitted on long drywall runs in ceilings (sketch at left) or walls, distances over 30 ft. Control joints may also be needed at common ceiling or wall stress points such as at 'L', 'T', 'U' or 'I' shape ceiling or wall intersections like those shown in our sketch above.
See DRYWALL CONTROL JOINTS
[Click to enlarge and show detail for any image]
Drywall tape type used for corners: do not use mesh type drywall tape in building corners nor at ceiling/wall joints. It may be easier to install than paper tape but it is not as strong and is more tear-prone.
Long runs of continuous drywall, especially if more than 30 feet or about 10 meters in its long dimension are likely to suffer expansion/contraction cracking and possibly ridging if control joints are omitted.
Our drywall ceiling photographs above and below show a continuous ceiling that runs the length of this home, or 64 1/2 feet in total distance.
The ceiling width is interrupted near one end by the distant partition wall you can see in the left hand photo, but the ceiling continues to open up into another room at that end of the house.
The ceiling crack shown in our photograph at above right occurs almost in the center of this long ceiling run. Seasonally as temperatures and humidity vary the width of this ceiling crack also changes from close to hairline (warm humid summer months) to nearly 1/8' in width (cold dry winter months).
Using the coefficients of thermal and moisture expansion and contraction in drywall found at PLASTERBOARD EXPANSION COEFFICIENTS, and with a 'ballpark' estimate of seasonal temperature variation of 20 degrees and relative humidity variation of 30%,
we calculate that the total expansion or contraction range force over this ceiling length (744 inches) is about 0.138' (thermal) and 0.145' (moisture) for a total of about 0.28 or 3/10 of an inch - more than a quarter of an inch - more than enough to cause a huge ceiling crack.
Why do we see that the actual ceiling crack is not nearly this wide?
Because the 744 inch long ceiling is not unrestrained while the coefficients of thermal and humidity expansion and shrinkage are for unrestrained gypsum board. This ceiling's gypsum board is nailed to the underside of flat roof rafters spaced 16' o.c., distributing much of the thermal and humidity-related expansion and contraction forces over a large area.
Still we see an ugly wintertime crack in this ceiling and a noticeable summertime crack as well. There is not much point in just taping over this crack without installing control joints in this ceiling.
Cracks In Ceiling Drywall Causes
Metal corner beads are more crack and separation prone in drywall installations than plastic tape-on or glue-on (using spray adhesive) or mud-on corner bead material.
Building foundation settlement, frost heave, foundation drainage contributions to gypsum board cracks & damage
Frost heaving foundations can cause differential movement in building walls that causes severe tearing or cracking in plasterboard, gypsum board, or drywall.
Photo above left: shear cracking shows up at the inside drywall corner of two exterior walls of a New York building.
This cracking was caused by differential frost heaving. At above right you can see the corresponding crack in masonry block foundation supporting the building walls. High soil water content, drainage difficulties, and freezing climate explain this damage.
See FOUNDATION CRACKS & DAMAGE GUIDE
Building framing shrinkage & framing quality contribution to gypsum board cracks & damage
Framing shrinkage & other snafus: using wet lumber, pressure treated and still wet lumber, or poor quality framing connections that permit movement and settlement that can in turn lead to drywall cracks, tears, or drywall joint tape separation.
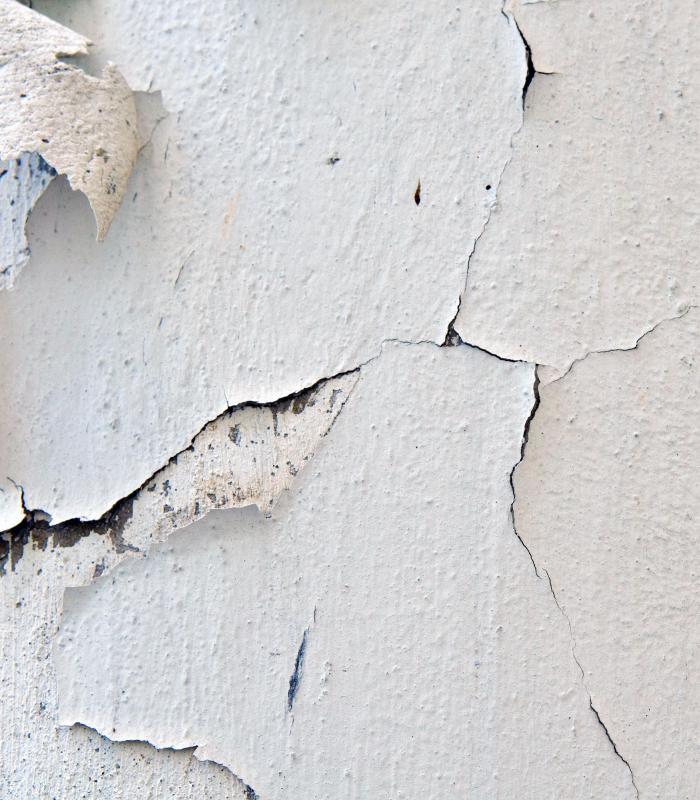
In a demonstration that the ceiling crack stress point sketch is not just theory, our photos just above show cracks at the taped intersection of ceiling to partition wall at a natural stress point. This crack appeared in less than a year after new construction.
The underlying cause may have been a combination of framing shrinkage and slight sagging of the supporting floor structure.
The wall corner projecting into the room is directly above a stairwell cutout. Floor settlement actually pulled this corner down, separating it from a rigid I-beam roof structure.
We will repair this crack by cutting out the separated paper drywall tape and re-taping the joint on both sides of the partition wall corner-to-ceiling juncture. But this little repair is a bit of trouble as re-painting the ceiling and wall will also be needed. In my OPINION (DF) this is normal new construction cracking that is difficult to prevent.
Our photo at left shows the original drywall being installed on the same ceiling as in the drywall tape joint separation photographs above.
You can see that the sheetrockers took care to hang a full piece of drywall that extended past the partition wall corner precisely because they knew that this was a stress point.
That detail worked - we did not see a tear in the drywall itself. What did ensue was enough downwards movement to stress and open the drywall tape at the partition wall-to-ceiling joint.
Below is a second example of a similar effect. Here we see a complex soffit structure carrying windows and suspended from a conventionally-framed 2x12 ceiling structure. Here, too, cracks appeared in the ceiling as the structure below moved downwards.
[Click to enlarge the photo at left to see this drywall ceiling crack in more detail].
Framing flexing - drywall cracks: in interior ceilings or cathedral-ceilings not framed to modern construction standards for stiffness we may see cracks, often at drywall joints, caused by flexing in the ceiling structure.
Particularly in some older homes with minimal attic floor framing that was originally intended only to support the weight of a plaster ceiling, we may see ceiling cracks caused by building occupants (or home inspectors) who clambered around in the attic area above, stepping on framing members never intended to bear their weight.
- Framing bowed, bent, uneven: installing drywall or gypsum board across uneven surfaces due to inconsistent or sloppy framing can add to material stresses that ultimately show up as plasterboard cracks.
Such cracks are most likely to appear when a side joint or end butt joint appear over or close to a framing variation extremity.
Use furring, cutting, trimming or similar measures to flatten out the install surface and to minimize these stresses, and avoid placing a taped joint over stress points. - Framing over-spanned: drywall installed at right angles to the supporting framing can span 24' (1/2' or 5/8' thick drywall) on walls, but on ceilings 1/2-inch or 5/8-inch drywall can span24 inches only if it is installed perpendicular to the joistsand supports less than 1.3 pounds per square foot (psf ) ofinsulation.
Otherwise, 16-inch on-center spacing is recommended.With latex spray textures or airless spraying oflatex paints, perpendicular installation over 16-inch on centerframing is recommended to prevent sagging. - S. Bliss, Best Drywall Practices - Roof truss uplift: arching roof or floor trusses caused by moisture/temperature differences between truss upper & lower members. The truss uplift problem is less likely to occur in an interior ceiling supporting a floor above because both sides of the ceiling/floor structure are within conditioned space, making for more uniform temperatures and moisture levels across the truss.
See TRUSS UPLIFT, ROOF for details.
Moisture or relative humidity variation contribution to gypsum board cracks & damage
Moisture or humidity variation: significant changes in the building moisture level or thus in the moisture content of plasterboard or gypsum board can cause expansion or shrinkage sufficient to produce a 1/16' wide or larger crack even if other forces are not in play.
Details of the coefficients of thermal expansion (or contraction) and the coefficients of moisture-related expansion and shrinkage of plasterboard are
at PLASTERBOARD EXPANSION COEFFICIENTS.
Structure or Foundation Settlement contribution to gypsum board cracks & damage
Settlement in buildings causes plasterboard cracks & tears: for any reason: framing shrinkage, foundation damage, site drainage problems, earthquake movement or slab settlement can cause significant gypsum board damage.
Below we give several examples of types of building movement traced to settlement and causing significant interior wall or ceiling cracking.
Backfill settlement in New York: the photographs below illustrate severe settlement in a New York home. Unlike the Alaskan house above (damaged by construction on thawing permafrost), the home below had been constructed on backfill over a stream bed.
Seasonal water flowing below the building appears to have contributed to severe slab and foundation damage that telegraphed upwards through this home as floor-wall separation, ceiling-wall separation, and cracks at windows and doors of the home shows in the photos just above.
By noting the plasterboard crack locations, patterns, angles, and dimensions it was apparent that they all pointed to settlement in the supporting slab.
Checking the finished basement floor for level we confirmed that the floor was settling significantly towards the building center.
Permafrost settlement in Alaska: The two photographs above show severe plasterboard cracking in the same Alaskan home illustrated at the top of this page.
In the above photo, settlement and drywall tearing cracks appeared at a horizontal drywall joint to the right of a door jamb (a poor location for a drywall joint and exacerbated by the use of mesh tape that is not as strong or tear resistant as paper tape).
[Click to enlarge and see detail for any image]
In our second drywal cracking photo just above we see a typical diagonal gypsum board crack extending down and to the left of a window opening.
The window trim has been pulled apart as well. These cracks are not to be blamed on the drywall installation: this home had suffered movement in excess of what plasterboard is expected to endure.
This building is discussed in more detail
at SINKING BUILDINGS.
Earthquake damage to walls in California:
Earthquake damage crack patterns characteristic of the Northridge earthquake in California in January 1994 are illustrated by our photo shown at left.
This crack pattern appears here in a stucco exterior, but it was duplicated on drywall interiors as well.
Buildings suffering this extent of damage require structural repair or possibly replacement.
Details are
at EARTHQUAKE DAMAGED FOUNDATIONS.
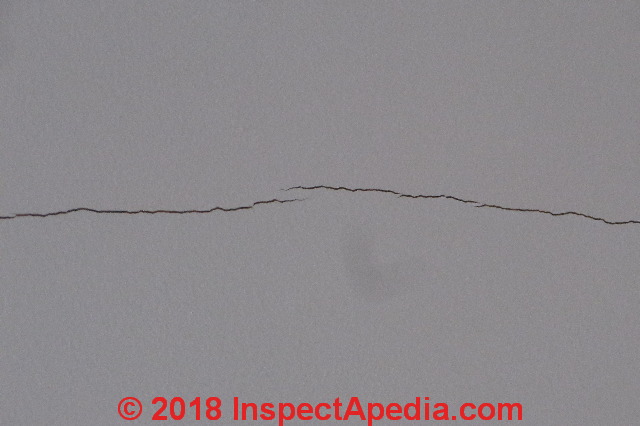
Temperature variation contribution to gypsum board cracks & damage
Temperature variation: significant changes in the building interior temperature or thus in the temperature of plasterboard or gypsum board can cause expansion or shrinkage sufficient to produce a 1/16' wide or larger crack even if other forces are not in play.
Even if building temperatures are kept steady after construction is complete, drywall installation temperatures may contribute to subsequent cracks: mudding drywall in cold buildings increases drying times and may increase the crack risk.
Large variations in building temperature or moisture level or both. For example, leaving a building un-heated in a freezing climate or turning off air conditioning & dehumidification in a wet or humid climate.
See HUMIDITY CONTROL & TARGETS INDOORS
and also DRYWALL MOLD TESTING.
Details are at PLASTERBOARD EXPANSION COEFFICIENTS.
How to Prevent Drywall Cracks at Drywall Side or End Butt Joints
Use kiln-dried lumber for framing walls and ceilings. As Steve Bliss points out
at DRYWALL INSTALLATION Best Practices, ' With wet or poor-quality framing, there are bound to be problems in the drywall finish. With dry lumber and proper detailing, however, drywall problems can be kept to a minimum.'
Use drywall screws instead of drywall nails. Set the screws just below the drywall paper surface but not so deep as to cut through the paper.
When hanging drywall on a ceiling supported by the lower chord of roof trusses, review the suggestions
at TRUSS UPLIFT, ROOF, including using clips rather than screws or nails to secure drywall within a few feet of either side of building center partitions that run at right angles to the lower chord of the roof trusses.
The floating drywall corner method described
at INTERIOR FINISHES: BEST PRACTICES can also be used to float the ceiling drywall over the center partitions.
Inside corners at walls and between walls and ceilings are stress points for drywall and common places for cracks or nail pops. Leaving one side of the joint free to move without fasteners will eliminate most of these problems.
On ceilings, place the first screws 7 to 12 inches in from the corner and support the ceiling drywall with the wall panels. Also, do not fasten the top 8 inches of the wall panels.
No screws should go into the top plate, where shrinkage may occur. Similarly, leave one side unfastened at wall-to-wall corners, but make sure it rests against solid wood backing or drywall clips (see Figure 5-1).
Prevent Drywall Cracks Caused by roof truss (or on occasion floor truss) uplift
Nail pops found in some building ceilings and actual tears or cracks at the wall/ceiling juncture at building walls located under the center of certain roof trusses when moisture & temperature differences between the truss bottom chord and upper members cause the truss to arch.
Details and more illustrations of the roof truss uplift problem & more steps to prevent drywall cracking & nail pops are found at
TRUSS UPLIFT, ROOF
The drawings of roof truss uplift and corrective measures for truss uplift shown here are provided courtesy of Carson Dunlop Associates and appears in their Illustrated Home.
Also see CEILING FINISHES INTERIOR
and
see BEST INTERIOR FINISH PRACTICES
GRC: Gypsum Board Joint Ridging & Cracking
Drywall / Gypsum Board / Plasterboard Butt-Joint Ridging Causes & Prevention
As this article series discusses the expansion and shrinkage effects of drywall or gypsum board ceilings and walls (plasterboard in the U.K., Australia, New Zealand and other countries), we include this description of cosmetic damage caused by expansion rather than material shrinkage stresses.
GRC or gypsum ridging and cracking has been reported world-wide, with most writers commenting from Australia, Canada, New Zealand, the U.K. and the U.S. [1][2][4]
[Click to enlarge any image]
The Gypsum Association's definition of ridging is
Joint ridging, also called beading, is a uniform, fine line deformation occurring at gypsum board joints.
It is usually caused by compression of the edges or ends of the finished and decorated gypsum board resulting from the edges or ends being forced together from exposure to alternating periods of high and low temperature and humidity extremes due to thermal or hygrometric expansion. - [10] Repair of Gypsum Board Joint Ridging ( GA-221-00 )
Note: both ridging and cracking in gypsum board may both appear in the same installation.
For example, ridging may appear when forces (thermal expansion, moisture expansion) cause the material to expand, while cracks or tears may appear in plasterboard or gypsum board when the opposite site conditions (cooler temperatures and more dry conditions) cause gypsum board to contract.
OPINION: As we note below, many experts opine that the dominant forces in drywall cracking or tears are probably framing shrinkage and building movement - a view with which I agree. However gypsum board joint ridging is almost certainly going to be due only to expansion forces alone and would be expected to appear particularly at long runs of unrelieved (no control joints) drywall exposed to high moisture and high temperature or the two combined.
Suggestions for preventing gypsum board ridging include:
- Inspect, document and correct building framing defects such as gaps, poor nailing or open framing joints before hanging the drywall.
- Do not hang gypsum board on wet or pressure treated framed ceilings or walls without special design provisions such as the use of resilient channel supports.
- Inspect, document, and correct site drainage, footing drain defects, building leaks and other sources of abnormal building moisture or of abnormal building movement, settlement, framing shrinkage.
- Manage building & gypsum board humidity and temperature: Document the building humidity and temperature at the time of drywall application [and we recommend documenting as well the actual temperature and humidity level or moisture level of the drywall product being installed), and document abnormal variations in building temperature and humidity indoors beyond its design parameters.
Gypsum board should be allowed to reach temperature and humidity consistent with the building interior where it is to be installed before it is hung or applied. - Additional measures to avoid ridging may include back-blocking or supporting at butt joints (extra cost, rarely used - DF)
- Repair recurrent problem areas by supporting drywall on resilient channels
- Use control joints at problem or stress points and in areas of drywall extending beyond 30 feet of unbroken or unrelieved panels.
- See the SBCA's detailed recommendations at 'Gypsum Joint Ridging and Cracking' [1]
Reader Q&A - also see the FAQs series linked-to below
On 2021-02-23 by (mod) - it's 'gypsym' wallboard, not 'Egyptian' wallboard.
@Kathy M,
I meant 'gypsum' wallboard as discussed in this article series.
Internet down, I was trying to reply using a cellphone and my phone is convinced it knows-better what I should be saying. (Nothing against Egyptians.)
On 2021-02-21 by Kathy M
Thanks Dan. I am not sure what Egyptian Board base is but will Google. Had a fire in 2015 in another part of the house and wondered if there may have been moisture in walls from where they hosed the house. or movement where we had to have some of the roof rebuilt. Also added 4 piers about 4 years ago so may have movement from that.I think I will get a home inspector to come look.
On 2021-02-04 - by (mod) -
My most complete advice that is more thorough than trying to make up an answer a new off the cuff is in the article above and others in this series so I hope that you will take a look.
I do notice however that in your photo we've lost what looks like a skim coat on an gypsum board base.
Or possiblywe are seeing the separation and peeling of painted-ove wallpaper that is no longer well-adhered to the gypsum board surface.
So it could be that the skim coating was not properly applied such as applying it over dust or dirt, or it could be that there's been a leak or moisture problem. Those are some things to look for.
Typically I find and remove all of the loose material on the wall by feeling for bubbles or bulges, cutting around the damage with a drywall knife, removing the loose material, skim-coating with joint compund to fill the damaged areas, sanding smooth, priming, and painting.
Watch out: working on old homes with painted-over wallpaper I've sometimes found that it's hard to stop removing loose surface material; particularly when we wet the edges of the removed area by the application of joint compound, more painted-wallpaper loosens its grip on the wall surface below.
If that problem is sufficiently widespread it's less costly and faster to laminate a new layer of 1/4' drywall over the whole wall than to keep fiddling with patching, taping, etc.
On 2021-01-31 by Kathy M
65 yr old house previously remodeled in 70's & 80's. Cracking/peeling walls,bubbles and nail pops. Cause? How to repair?
[Photo above]
On 2020-10-13 - by (mod) -
Steve
Thanks so much for the comment: hearing from pros in the field is particularly helpful to everyone.
Before prescribing a repair or preventive measures for the ceiling-wall crack, if we can diagnose the cause with confidence we'll be more certain of the repair.
It's possible that you are seeing the infamous 'rising roof truss' crack that occurs at an interior partition wall/ceiling juncture. In particular this crack shows up between ceiling and wall of a wall that is close to the middle of a building and runs parallel to the front and rear walls or roof eaves, AND where the roof is supported by trusses.
That problem occurs because of differences in arching of the truss upper and lower components that in turn are because the truss bottom chord that supports the drywall ceiling is buried in insulation.
The 'fix' is to eliminate the screws or nails securing the drywall to the ceiling for a couple of feet on either side of that interior partition wall. In bad cases where the drywall is sufficiently damaged as to justify demolition and re-work, there are special clips that are used to hold the drywall to the wall top instead of the truss bottoms near the building center.
None of that repair needs to be done from that cramped attic;
Where I've fixed these cracks I either removed ceiling drywall screws that were into the truss bottom chord for a couple of feet on either side of the center partition wall or if nails were used, I use a punch to drive the nails all the way into the truss bottom, then patch the hole left in the ceiling and re-paint.
A second cause of cracking in the ceilling drywall may come from people or heavy storage over the area of damage - in particular when the ceiling is framed with minimal sized lumber; I've found this in cottages built in North America, the UK and Spain that date from the 1940s and 50s. But those areas of damage are different: the damage occurs closer to the center of the span, not right over the middle partition wall.
As it will help others and might encourage some useful comment, I will RE-POST this discussion over at
TRUSS UPLIFT, ROOF
And I'll be grateful if you can post a photo or if you have further comments, criticism, or suggestions.
On 2020-10-13 by Steve
As a drywaller i see a lot of cracks on ceilings. That begin at a outside corner interior wall. And extend across most of the room's ceiling. I figure the cause is movement in ceiling rafters. Where one is extended across the entire distance of the exterior walls and the one next to it is supported by interior upper wall plates . the crack starts at these supported locations and extend across the distance of all the unsupported joists. Because stiffeners were not put in place to keep bowing from occuring
How can this problem be best corrected with minimul actic space to work in.
On 2020-05-13 by (mod) - common causes/cures for drywall cracks at a window
Brad
Thanks for an interesting and helpful question that I'd phrase as: Interior details to permit and cover drywall crack from cyclic building movement.
Given the location of the crasck and the surrounding framing deign, I don't assume this drywall cracking and wall movement are due to foundation settlement nor expansive soils etc.
First: in my experience cracking at a location like the one shown in your photo - where there is an intersecting roof plane that can be difficult to tie to the main structure, and where there is a framed opening for a window (where header connections are critical) it's not a surprise to find evidence of movement.
The underlying problem could be inadequate header at the window, inadequate connections of the lower sloped-roof to the main structure, or a similar problem.
Second: expansive clay soils can damage more than drywall, also moving and damaging foundations and in extreme cases, plumbing connections. So it is worth investigating whether a soil watering or de-watering system, such as commonly used under buildings with expensive clay soils, is necessary and would be helpful.
Third : In the location shown in your photo, it would be easy to add wooden trim that is fastened only on one side of the moving wall. That would cover the crack and allow movement without any visual evidence in the room. You'll need to extend the trim and include it in the interior design for it to make sense. f
Watch out: Before pretending to repair the window cracks I'd want to be confident that there is no other movement in the structure that needs repair and that might indicate more serious need for improved structural connections of roof or window header.
If you are confident that there is no significant underlying structural concern, then a cosmetic approach is fine.
For areas of less total movement I've used reinforced mesh tape before taping over and repairing crack damage.
In some locations indoors, such as at a wall-ceiling juncture, we use clips to carry the drywall so that the building can move without telegraphing that movement into drywall cracks. Those clips are described in our article that discusses cracks caused by rising roof trusses. See
details at TRUSS UPLIFT, ROOF
Thanks for asking - let me know what questions or thoughts occur to you on this.
On 2020-05-13 by Brad Sherman
[Regarding the photo shown above]
Differential building settlement, a change in building materials (standard timber frame / brick pier for original house and thermacell polystyrene / concrete for new work on big concrete footings), and stress concentration at the window corner have contributed to this crack.
At one stage it opened and I filled the gap and repainted. It subsequently contracted and squeezed out my earlier repair. Now it’s opened up again. I would just like to straighten the lines and make things look more ‘planned’ because the clay soils here mean the expansion/contraction cycle will continue.
Can you advise what sort of approach is best suited to lessen the visual impact of inevitable future building movement?
On 2020-02-03 - by (mod) -
Susan
You ask a perfectly reasonable question but from just your text I don't know what's going on.
I use the 'fear-o-meter' approach to decide how to act on questions like this.
What else can we find that raises or lowers our level of concern?
At what point do we cross an action threshold: or when do we cross the line between: keep an eye on it - and cut an opening or do other invasive inspection?
If there's no water entry, no mold, no smells, no signs of structural movement, you might wait to act.
To know for certain what's happening you'd need to remove the drywall (as less troublesome than digging up the foundation, a step that can cause its own problems).
Outside, keep roof runoff and surface runoff away from the foundation.
Search InspectApedia.com for FOUNDATION CRACK DAMAGE to see more detail.
On 2020-02-01 by Susan Swan
I have an almost 50 year old back split home, with the lower level is about 50% underground. The bottom of the windows in the downstairs at right at ground level. I just discovered a horizontal crack about 1/2 an inch under the window running the length of the window. The windows are probably 25 years old. Should I be worried that it is the foundation? The wall doesn't have any water stains and it doesn't smell mildewy in the area.
Question: how to repair cracked RhinoBoard
2017/08/31 Hennie said:
I have a flat roof and have problems with cracking and peeling ceilings. How do you repair it. It is Rhinoboard. Please help
Reply: first diagnose the cause of damage and decide if other building repairs are needed
Hennie,
Before suggesting a repair we want to know the cause of the cracking and we need to know (we meaning you mostly with some encouragement from the sidelines) if there is damage to the structure behind those cracks.
Otherwise a cosmetic repair may be wasted and a more-serious problem such as a leak, structural damage from loading, rot, or insects, may need to be repaired.
If you're using the RhinoBoard that's a product of GypRock Staint Gobain in South Africa (or similar) we're talking about a plasterboard that uses a foamed or aerated gypsum core bonded to paper liners: ivory coloured on one side and tan-brown on the other. Rhinoboard is non-combustible and is used on ceilings and walls.
Rhinoboard is sold square-edged and in tapered-edge formats, the latter making it easier to tape and plaster over joints before painting in what the manufacturer calls a monolithic finish as in the Gyproc Drywall System.
So you could remove peeled loose coating, skim coat the peeled areas with joint compound, then tape cracks and joints using a fibreglass mesh tape, then coat with joint compound out 18' wide across the crack to hide the damage.
But as I intended to emphasize that work would be wasted if we don't first diagnose the cause of the trouble you are seeing.
Besides cracking, the peeling could be telling us there are roof leaks to be found and repaired, and it could hint that there is a mold reservoir in the roof cavity. If I were repairing a Rhinoboard ceiling with those conditions I would
- make a test cut into the ceiling to inspect for water, leaks, mold, in the most-damaged, most-suspect areas.
- inspect the roof for leaks
- hold off on cosmetic repairs until those questions are answered.
If your Rhinoboard is suffering from recurrent cracks that have been repaired before, and if there are no building leaks above, then
see DRYWALL CONTROL JOINTS
Also see our discussion of drywall cracks and nail pops repairs
at DRYWALL NAIL POPS
If you want to send me photos of the condition for comment use the page top or bottom CONTACT link and I may have more specific advice I can offer. Also it would help to know the country and city where your building is located.
- RHINOBOARD for CEILINGS, [PDF] Gyhproc Saint Gobain, 1 Shale Rd,N1 Business park,Intersection of Old JHB Rd and Tlokwa Street, Kosmosdal, Centurion, South Africa, Tel: +27 12 657 2800, Customer contact centre, 0860 27 28 29, Website: www.gyproc.co.za,or www.isover.co.za etrieved 2017/08/31, original source: http://www.gyproc.co.za/products/walls/rhinoboard
RhinoBoard Square-Edge produced by Gyproc SA is a fire-resistant ceiling material with the following specifications, excerpted from the company's web page cited below:
Subject to loading detail, suspension should not exceed 1200mm centres
The suspension must not be out of plumb (vertical) more than 25mm for each 150mm of plenum depth and in no case should exceed 500mm to a 3000mm depth
Whenever the above is exceeded and/or when the hanger suspension is more than 2000mm long, then a sub grid is recommended. Should suspension be vertical, then a 4200mm drop would be acceptable using hanger strap
In no case should suspension be from other services in the ceiling void
A hanger suspension point within 400mm from the wall angle or shadow moulding must be installed on main tees and cross tees
Two steel pop rivets with a shear strength three times that of the maximum allowed ceiling load is to be used
When securing wire to tee, it should be wound tightly around itself at least three times
Should the ceiling mass exceed 20kg/m2, a sub grid is required and a consulting engineer should recommend suitable suspension - retrieved 2017/09/01, original source: http://www.gyproc.co.za/products/ceilings/rhinoboard-0 - A distinctly different product, Rhino Board™, is a polypropylene honeycomb sheet made of cylindrical polyolefin tube straws bonded into a close-packed hexagonal matrix to produce a low bulk density material manufactured in a proprietary process by Rhinoboardwj, 2711 Karsten Court SE, Albuquerque, NM 87102 USA, Tel: (505) 842-5100, Email: info@rhinoboardwj.com, also distributed in Europe.
A tpical use of this Rhino Board™ product is service as ' a lightweight and durable cutting surface for abrasive or straight sater jet cutting' . Website: http://www.rhinoboardwj.com/
...
Continue reading at DRYWALL CONTROL JOINTS or select a topic from the closely-related articles below, or see the complete ARTICLE INDEX.
Or see DRYWALL CRACK CAUSE FAQs - questions & answers posted originally here
Or see these
Drywall / Gypsum Board Articles
- DRYWALL, FIBERBOARD, PLASTER INTERIORS - home
Suggested citation for this web page
DRYWALL CRACK CAUSES at InspectApedia.com - online encyclopedia of building & environmental inspection, testing, diagnosis, repair, & problem prevention advice.
Or see this
INDEX to RELATED ARTICLES: ARTICLE INDEX to BUILDING INTERIORS
Or use the SEARCH BOX found below to Ask a Question or Search InspectApedia
...
Ask a Question or Search InspectApedia
Try the search box just below, or if you prefer, post a question or comment in the Comments box below and we will respond promptly.
Search the InspectApedia website
Note: appearance of your Comment below may be delayed:if your comment contains an image, web link, or text that looks to the software as if it might be a web link, your posting will appear after it has been approved by a moderator. Apologies for the delay.
Technical Reviewers & References
- [1] 'Gypsum Joint Ridging and Cracking', (2009), SBCA Tech Notes, Structural Building Components Association, 6300 Enterprise LaneMadison WI 53719, (608) 274-4849, (608) 274-3329 FAX, retrieved 12/11/2013, original source http://support.sbcindustry.com/images/technotes/T-GypsumInstallation09.pdf
- [1a] Paul F. Schofield, Kevin S. Knight, Iona C. Stretrton, 'Thermal Expansion of gypsum investigated by neutron powder diffraction', (1996) Manuscript, retrieved 12/11/2013, original source: http://www.minsocam.org/msa/ammin/toc/ Articles_Free/1996/Schofield_p847-851_96.pdf
- [1b] Azree Othman Mydin, 'Gypsum Board Thermal Properties Exposed to High Temperature and Fire Condition', (2012), University Sains Malaysia School of Housing Building and Planning, retrieved 12/11/2013, original source: http://www.ce.tuiasi.ro/~bipcons/Archive/325.pdf
- [2] 'Gypsum Board Typical Mechanical And Physical Properties (GA-235-10)', (2010) Gypsum Association, 6525 Belcrest Road, Suite 480, Hyattsville MD 20782, retrieved 12/11/2013, original source: http://www.gypsum.org/wp/wp-content/uploads/2011/11/GA-235-10.pdf
- [3] Drywall or plasterboard standards: ASTM D3678
- Drywall or plasterboard standards: ASTM C1047
- Drywall or plasterboard standards: ASTM D4216-99
- Drywall or plasterboard standards: Canadian Codes [pending CSA citations]
- ASTM C 473 specifies the maximum deflection in humidified gypsum board for interiors, for ceiling board, and for exterior gypsum soffit board
- Drywall or plasterboard standards: ASTM C840
- Drywall or plasterboard standards: ASTM C844
- Drywall or plasterboard standards: Gypsum Association GA -216
- Drywall or plasterboard standards: Gypsum Association GA -234 (Fire-Resistant Applications)
- Drywall or plasterboard standards: Australian Standard AS2311–1992 for The Painting of Buildings (when painting plasterboard walls & ceilings)
- [4] Boral Plasterboard (Australia), 'Boral Plasterboard Installation Manual', August 2007, PB103, Tel: 1800-811 222 (in Australia), Email: tecassist@boral.com.au, Website: www.boral.com.au, ACT: 7 Barrier St, Fyshwick 2609, Tel: 02 6280-4243. Other Boral Plasterboard offices are in New South Wales, Northern Territory, Queensland, South Australia, Tasmania, Victoria, Western Australia, and the company has an export department.
- [4a] Boral, 'Plasterboard Specifications', retrieved 12/11/2013, original source: http://www.boral.com.au/plasterboardexport/ plasterboard_specifications.asp
- [5] British Gypsum Co., 'Gyproc Control Joint, Products Plasterboard Accessories', Website: www.british-gypsum.com.
- [6] George M. Kutcher, Jr., 'Don't Overlook Control Joints in Drywall Construction', National Gypsum Company, Tel: 1-800-NATIONAL, www.nationalgypsum.com, retrieved 12/10/13, original source: http://www.nationalgypsum.com/resources/tech-talk-controljoint.htm
- [7] National Gypsum Company, 'Gypsum Board Systems', 12th Ed., (2000), (Gold Bond® brand gypsumboard products), website: http://www.nationalgypsum.com
- [8] George M. Kutcher, Jr., 'Don't Overlook Control Joints in Drywall Construction', National Gypsum Company, retrieved 12/10/2013, original soruce: http://www.nationalgypsum.com/resources /tech-talk-controljoint.htm
- [9] 'Design Essentials for Controlling Movement Induced Stresses in Building Materials', Winstone Wallboards, Ltd., Winstone Gypsum, Dec. 2009, Winstone Wallboards Ltd 219 Opawa Road PO Box 1983 Christchurch New Zealand Phone: +64-3-332-3159, and Winstone Wallboards Ltd 37 Felix St PO Box 12-256 Penrose Auckland New Zealand, Tel: +64-9-633-0100, Email: gypsum@gib.co.nz, Toll free: 0800 475 475.
Note: per Winstone: for large ceilings, AS/NZS 2589 specifies that all sheet end butt joints are backblocked (to reinforce the joint where such joints are not meeting over a ceiling joist). [This is a reinforcement detail for unsupported butt joints, not a wallboard movement control joint detail. The company's article does recommend that installers insert control joints at the junction of wallboard ceilings at hallways vs large open spaces - Ed. ]- Cracking and Building Movement, Dickinson & Thornton, 2006
- BRANZ Bulletin 418 July 2001 ’Providing for Thermal and Moisture Movement’
- Cracking and Building Movement, Dickinson & Thornton, 2006
- NZS 3602 Timber & Wood Based Products for use in Building
- Wood Processing Newsletter SCION July 2003 Simpson & Turner
- ‘A Field Study of moisture performance of roofs etc.’ Technical Report 127. 1994 Cunningham et al
- ‘Plasterboard Peaking and Cracking under Timber R oof Trusses’ 1999 - Prof H Robert Milner, BE, MEngSc, PhD, FIEAust, AIWSc and CY Adam, BE, MEngSC Monash Engineering Timber Centre, Monash University, Australia
- ‘Walls & Ceilings’ Magazine ‘Drywall Cracking on a Global Scale’ By Greg Campbell March 9, 2001 ix AS/NZS2589 2007 – Gypsum Linings - Application & Finishing
- [10] Repair of Gypsum Board Joint Ridging ( GA-221-00 )
- [11] Eric Galow, Galow Homes, Lagrangeville, NY. Mr. Galow can be reached by email: ericgalow@gmail.com or by telephone: 914-474-6613. Mr. Galow specializes in residential construction including both new homes and repairs, renovations, and additions.
- [12] 'Finishing Drywall Systems', U.S. Gypsum (USG) Corporation [copy on file as USG_Finishing_Drywall_Systems_Ch5.pdf] 2009
- [13] 'Sheetrock® All Purpose Joint Compound - Select for professional drywall finishing', Submittal Sheet 09250
- [14] 'Quality Drywall Finishing in All Kinds of Weather', USG Folder J-75 (out of print), U.S. Gypsum corporation
- [15] Gypsum Construction Guide, National Gypsum Corporation
- [16] Gypsum Construction Handbook [purchase at Amazon.com] H17, Technical Folder SA920 and PM2, PM3 and PM4, United States Gypsum Company, 125 South Franklin ST., PO Box 806278, Chicago, IL 60680-4124,
- [16a] R.S. Means, The Gypsum Construction Handbook, 6th Ed., J. Wiley, (2009), ISBN 978-0-87629-258-7, quoting J. Wiley & Sons:
One of the construction industry's longest-running, most relied-on references, The Gypsum Construction Handbook was first published by the U.S. Gypsum Company in 1904. For more than a century and through several editions, the book has become a trusted standard. This new 6th edition is an illustrated, comprehensive, and authoritative guide on all facets of gypsum construction.You'll find the newest product developments, installation methods, fire- and sound-rated construction information, illustrated framing-to-finish application instructions, estimating and planning information, and more. System descriptions – together with full data on products, accessories, tools, equipment, and applications – help plan and estimate projects and ensure compliance with performance criteria.Cost- and time-saving techniques keep the work on budget. New in the sixth edition are chapters on sustainable construction methods and products, building movement, fire resistance, heat transfer, sound transmission, and vapor/moisture control.The Handbook covers both new construction and repair and remodeling and includes: framing drywall and veneer plaster joint treatment and plaster finishing interior cement board ceilings conventional plaster - [16b] Gypsum Construction Handbook [purchase at Amazon.com] H17, Technical Folder SA920 and PM2, PM3 and PM4, United States Gypsum Company, 125 South Franklin ST., PO Box 806278, Chicago, IL 60680-4124,
- [17] Lath & Plaster Systems [copy on file as /interiors/LathPlaster_Nat_Gypsum.pdf ] - , 092300/NGC, National Gypsum Lath and Plaster Systems, National Gypsum Corporation, 800-628-4662 describing National Gypsum's Kal-Kore brand plaster base
- [18] Metal Lath Specifications, Specification for metal lath and accessories, Lath and Plaster [copy on file as/interiors/Amico_lath-inside.pdf ] - from Amico, a lath and plaster accessory producer.
- [19] Plastering, PM 5, Product & Systems Technology, US Gypsum, May 1998, web search 10.5.2010, original source: http://www.usg.com/rc/technical-articles/plaster/ [copy on file as/interiors/Plastering_USG.pdf ] -
plastering-technical-guide-veneer-plaster-joint-reinforcement-systems-en-PM5.pdf
United States Gypsum Company, 125 South Franklin ST., PO Box 806278, Chicago, IL 60680-4124,
Paraphrasing from this document: USG uses the term shadowing in this document in describing the visual effect over gypsum board joints caused by the lower moisture absorption rate (take-up) and lower capacity than gypsum base face paper. Shadowing at joints occurs where veneer plaster is applied over tape joints, requiring a second coat to completely hide the tape, providing a visually uniform surface. USG Advises: 'This [second] cover coat must be allowed to harden and dry before plaster application is started. - [20] Plastering Skills, F. Van Den Branden, Thomas L. Hartsell, Amer Technical Pub (July 1, 1985), ISBN-10: 0826906575, ISBN-13: 978-0826906571 [purchase at Amazon.com]
- [21] Drywall Finishing Council www.dwfc.org, Members: CertainTeed Gypsum • Freeman Products • Georgia Pacific Gypsum LLC • LaFarge North America • Magnum Products • National Gypsum Company • Panel Rey SA • Rapid Set Cement • Saint-Gobain, Inc • Sherwin-Williams Company • Solid Products, Inc. • Southern Wall Products • Trim-Tex, Inc. • United States Gypsum Company • Westpac Materials
- 'Joint Compound Drying Time, the Impact of Environmental Conditions', Drywall Finishing Council, Retrieved 8/16/12, original source: http://www.dwfc.org/wp-content/files/2010_03_16_Joint_Compound_Drying.pdf [copy on file as Joint_Compound_Dry_Tmie_DWC.pdf]
- 'Jobsite Conditions for Applying Interior Finishing Materials', Drywall Finishing Council, Retrieved 8/16/12, original source: http://www.dwfc.org/wp-content/files/2011_09_16_Interior_Job_Condition_Specifications.pdf [copy on file as Drywall_Finish_Conditions_DWC.pdf ]
- DWFC. Interior Job Condition Specifications For The Application of Drywall Joint Compounds,
Drywall Textures, and Paint/Coatings'. Drywall Finishing Council, Incorporated. www.dwfc.org - DWFC. Recommended Specification for Preparations of Gypsum Board Surfaces Prior To Texture
Application, Drywall Finishing Council, Incorporated. www.dwfc.org - GA. GA-214, Recommended Levels of Gypsum Board Finish. Gypsum Association, 6525 Belcrest
Road - Suite 480. Hyattsville, MD 20782 www.gypsum.org - National Gypsum Company. ProForm Brand Drywall Finishing Products Construction Guide,
National Gypsum Company, 2001 Rexford Road, Charlotte, NC, 28211, www.nationalgypsum.com
- [22] The Gypsum Association www.gypsum.org Gypsum Construction Handbook H-17 [purchase at Amazon.com] . USG Corporation, 550 West Adams Street, Chicago, IL, 60661, www.usg.com
- [23] Painting and Decorating Contractors of America www.pdca.org Smartwood/Rainforest Alliance www.smartwood.org
- [24] 'Joint Compounds', United States Gypsum Company, 125 South Franklin ST., PO Box 806278, Chicago, IL 60680-4124, retrieved 8/16/12, original source: http://www.usg.com/interiors/joint-compounds.html [copy on file as Mud_Types_USG.pdf]
- [25] Gypsum Construction Guide, National Gypsum Corporation
- [26]
- [27] Lath & Plaster Systems, 092300/NGC, National Gypsum Lath and Plaster Systems, National Gypsum Corporation, 800-628-4662 describing National Gypsum's Kal-Kore brand plaster base
- [28] Metal Lath Specifications, Specification for metal lath and accessories, Lath and Plaster from Amico, a lath and plaster accessory producer.
- [29] Plastering Skills, F. Van Den Branden, Thomas L. Hartsell, Amer Technical Pub (July 1, 1985), ISBN-10: 0826906575, ISBN-13: 978-0826906571 [purchase at Amazon.com]
- [30] Plastering, PM 5, Product & Systems Technology, US Gypsum, May 1998, web search 10.5.2010, original source: http://www.usg.com/rc/technical-articles/plaster/
plastering-technical-guide-veneer-plaster-joint-reinforcement-systems-en-PM5.pdf
United States Gypsum Company, 125 South Franklin ST., PO Box 806278, Chicago, IL 60680-4124,
Paraphrasing from this document: USG uses the term shadowing in this document in describing the visual effect over gypsum board joints caused by the lower moisture absorption rate (take-up) and lower capacity than gypsum base face paper. Shadowing at joints occurs where veneer plaster is applied over tape joints, requiring a second coat to completely hide the tape, providing a visually uniform surface. USG Advises: 'This [second] cover coat must be allowed to harden and dry before plaster application is started. - ...
How To Repair Cracks In Drywall Ceiling
Books & Articles on Building & Environmental Inspection, Testing, Diagnosis, & Repair
- Our recommended books about building & mechanical systems design, inspection, problem diagnosis, and repair, and about indoor environment and IAQ testing, diagnosis, and cleanup are at the InspectAPedia Bookstore. Also see our Book Reviews - InspectAPedia.
- Gypsum Construction Handbook [purchase at Amazon.com] H17, Technical Folder SA920 and PM2, PM3 and PM4, United States Gypsum Company, 125 South Franklin ST., PO Box 806278, Chicago, IL 60680-4124,
- ...
- Carson, Dunlop & Associates Ltd., 120 Carlton Street Suite 407, Toronto ON M5A 4K2. Tel: (416) 964-9415 1-800-268-7070 Email: info@carsondunlop.com. The firm provides professional HOME INSPECTION SERVICES and also extensive HOME INSPECTION EDUCATION and home inspection-related PUBLICATIONS. Alan Carson is a past president of ASHI, the American Society of Home Inspectors.
Thanks to Alan Carson and Bob Dunlop, for permission for InspectAPedia to use text excerpts from The Home Reference Book & illustrations from The Illustrated Home. Carson Dunlop Associates' provides extensive home inspection education and report writing material.
The ILLUSTRATED HOME illustrates construction details and building components, a reference for owners & inspectors.
Special Offer: For a 5% discount on any number of copies of the Illustrated Home purchased as a single order Enter INSPECTAILL in the order payment page 'Promo/Redemption' space.
TECHNICAL REFERENCE GUIDE to manufacturer's model and serial number information for heating and cooling equipment, useful for determining the age of heating boilers, furnaces, water heaters is provided by Carson Dunlop Weldon & Associates
Special Offer: Carson Dunlop Associates offers InspectAPedia readers in the U.S.A. a 5% discount on any number of copies of the Technical Reference Guide purchased as a single order. Just enter INSPECTATRG in the order payment page 'Promo/Redemption' space. - The HOME REFERENCE BOOK - the Encyclopedia of Homes, Carson Dunlop & Associates, Toronto, Ontario, 25th Ed., 2012, is a bound volume of more than 450 illustrated pages that assist home inspectors and home owners in the inspection and detection of problems on buildings. The text is intended as a reference guide to help building owners operate and maintain their home effectively. Field inspection worksheets are included at the back of the volume.
Special Offer: For a 10% discount on any number of copies of the Home Reference Book purchased as a single order. Enter INSPECTAHRB in the order payment page 'Promo/Redemption' space. InspectAPedia.com editor Daniel Friedman is a contributing author.
Or choose the The HOME REFERENCE eBook for PCs, Macs, Kindle, iPad, iPhone, or Android Smart Phones.
Special Offer: For a 5% discount on any number of copies of the Home Reference eBook purchased as a single order. Enter INSPECTAEHRB in the order payment page 'Promo/Redemption' space. - Building inspection education & report writing systems from Carson, Dunlop & Associates Ltd
COMMERCIAL BUILDING INSPECTION COURSES - protocol ASTM Standard E 2018-08 for Property Condition Assessments
HOME INSPECTION EDUCATION COURESES (Canada)
HOME INSPECTION EDUCATION COURSES (USA) including home study & live classes at eleven colleges & universities.
HOME INSPECTION EDUCATION: HOME STUDY COURSES - ASHI@Home Training 10-course program.
Special Offer: Carson Dunlop Associates offers InspectAPedia readers in the U.S.A. a 5% discount on these courses: Enter INSPECTAHITP in the order payment page 'Promo/Redemption' space. InspectAPedia.com editor Daniel Friedman is a contributing author. - The Horizon Software System manages business operations,scheduling, & inspection report writing using Carson Dunlop's knowledge base & color images. The Horizon system runs on always-available cloud-based software for office computers, laptops, tablets, iPad, Android, & other smartphones